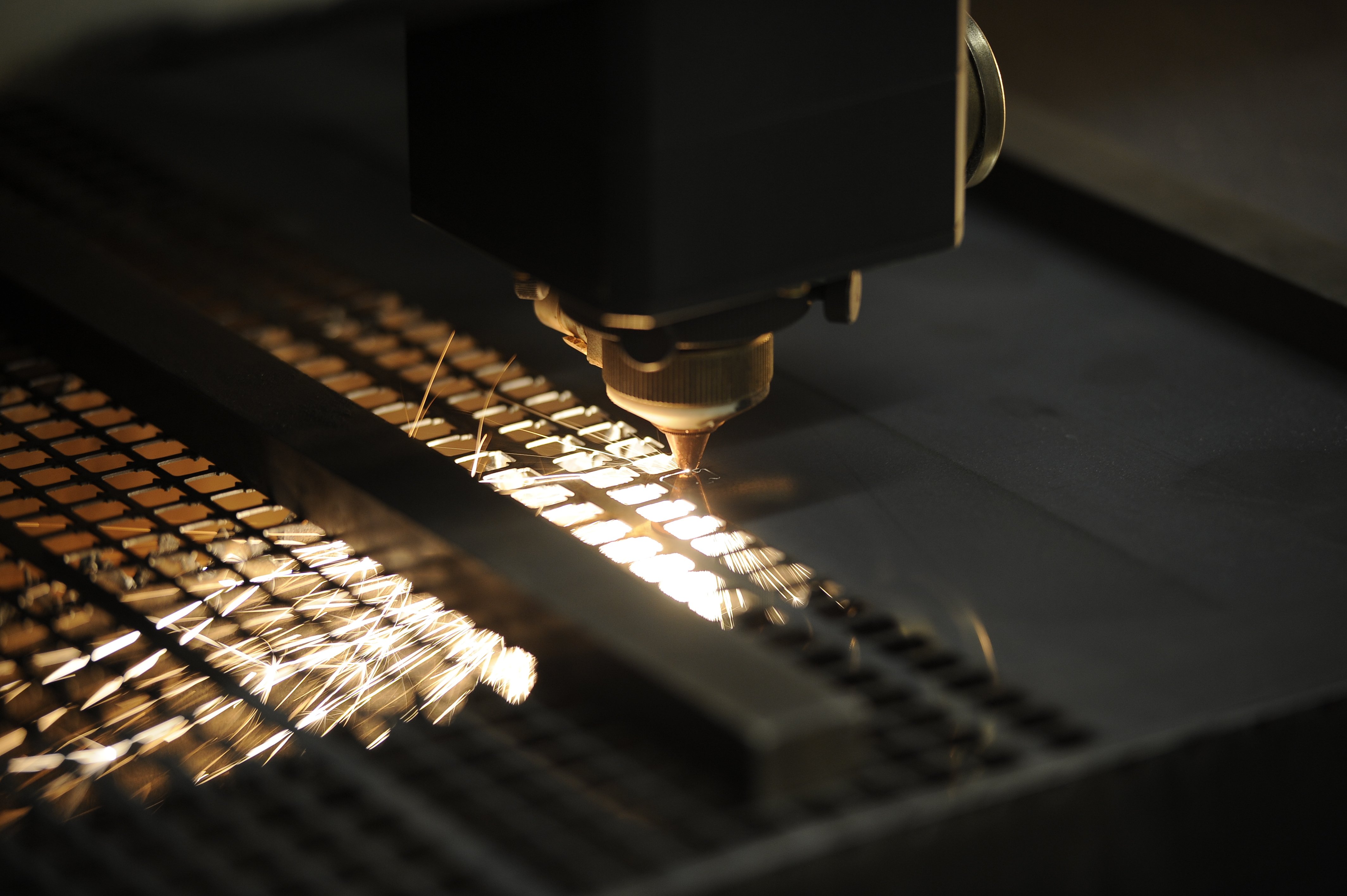
Laser cutting is a technology that uses high-powered lasers to cut through materials. A variety of industrial manufacturers depend on laser cutting’s precision, versatility, and cost-effectiveness to cut a range of materials for components.
Metalcraft Solutions utilizes laser cutting technology to process sheet metal, rubber, and plastics. The two most common alternative technologies on the market include plasma and water jet cutting. Depending on the component’s size and needed precision, or urgency of the order, one cutting method may be better than the other. Continue reading below as we explore laser cutting, plasma cutting, and water jetting.
Businesses choose Metalcraft Solutions’ laser cutting services for precision, versatility, and speed. Laser cutting is an ideal option for a variety of industries, including:
It’s a prominent component in sheet metal manufacturing, allowing you to pivot from one size and shape to another in the same setup. Geometries can be nested together on the same sheet for efficient material consumption, which saves time and money.
Metalcraft Solutions offers two types of laser cutting: CO2 and fiber optic.
However, there are a few types of material that due to their ability to reflect the laser beam back into the machine, cannot be used with this type of laser cutter.
Fiber Optic Laser Cutting
Fiber optic laser cutting is a relatively recent development, delivering an even cleaner cut. Diodes channel the laser through fiber optic cables and amplify it, delivering a remarkably precise laser to cut more reflective materials including:
Each type of laser cutter has its limitations. Thicker metals and plates are often too strong for either method, making laser cutting an impractical choice for some components. While this is dependent on the type of machinery used, it’s wise to explore other methods or to speak with a specialist before choosing laser cutting.
For an exceptionally fast process, plasma cutting is often the preferred method for a range of industries and components. While the process is similar to laser cutting, it doesn’t deliver the same accuracy and cost-effectiveness.
Consider plasma cutting the “roughneck” method of cutting: It trades accuracy for speed, with the ability to crudely cut inch-thick metal with relative ease. While this method isn’t the right option for those who require precise, intricate cuts, it’s an excellent option for components that will experience wear and tear once complete, including installation in:
While laser cutting and plasma cutting are excellent options for cutting different types of metal, water jetting is a great choice for cutting non-metallic materials, including:
But much like plasma cutting, water jetting sacrifices accuracy for speed, making it somewhat limited with the types of cuts it offers. This is especially true for thicker cuts. Water Jetting is best suited for thinner cuts and can often deliver a large order faster than laser cutting.
Whether you need to quickly fill a high-volume order or need a limited run of exceptionally intricate components, we have the materials and capabilities to complete your order on time and within budget.
Reach out to us today to talk about your project with one of our experts. With several machining capabilities under one roof, we can help you with each phase of your project and ensure you find the right materials or processes for your needs.
325 Morgan Ave.
Akron, Ohio 44311
330-773-5173